“Aluminum or steel?” This is the question often asked by clients during the design phase of parts development. The differences between aluminum and steel in terms of strength, processability, corrosion resistance, cost, etc., are so varied that simply stating which material is better is difficult. At Dynaox, the majority of our customers end up selecting aluminum rather than steel or stainless steel. In this newsletter we would like to provide you with the basic information about various aluminum materials in order to help you when you need to find the right material for your application.
Aluminum Properties
The specific gravity of aluminum is about 35% that of steel, and this makes aluminum easy to handle due to its light weight. Aluminum also has satisfactory electrical conductivity and some corrosion resistance characteristics because of the oxide film formed on its surface.
Aluminum is commonly used in heat exchangers, engine parts, and air-conditioners due to its high Thermal conductivity properties. Thermal conductivity ratings of metal materials are: 1) silver (428), 2) copper (403), 3) gold (320), 4) aluminum (236). Steel is 84 and stainless-steel is (17-21)*. As you can see, aluminum is optimum among general metal materials when high thermal conductivity and low cost are required.
( For comparison, air is 0.0241 and water is 0.582)
* Unit in (W/mk) and numbers are reference only.
Aluminum alloys
Aluminum is widely used for various common purposes from food and beverage cans, to housing components of home appliances and building materials such as window frames.
However, items utilizing 100% pure aluminum (like a one yen coin) are rare, and most of the Aluminum material used in products is an aluminum alloy.
While aluminum alloys still take advantage of the light weight and conductive properties of aluminum, other properties such as strength can be greatly improved for wider range of uses.
There are two basic types of aluminum alloy: wrought alloy (sheet, strip, pipe, stick, and coiled shape from rolling, extruding, drawing, and forging process), and cast alloy.
At Dynaox, we primarily handle wrought alloy materials.
Wrought type alloys come in non-heat-treatable and heat-treatable aluminum forms. Characteristic and usage of each are as follows:
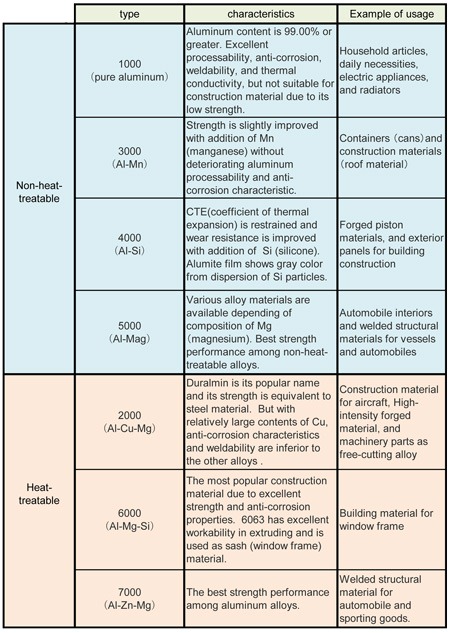
Characteristics of aluminum alloy vary depending on the amount and composition of added elements. Desired performance, processability, and cost are also factors in deciding which alloy will be suitable material for your requirements.
Special aluminum alloy
5000 is the most popularly used material with a moderate level of strength. CM10 and YM3007 are also recommendable special material for improved thermal conductivity and additional strength.
How to process the material
There are various types of processes depending on a required shape. Some specific processes restrict the material to be used. The common materials Dynaox handles are listed below.
1) Extruded pipe material : A6063, A5052, A5056, CM10, YM3007, etc.
* Only porthole pipes in China
2) Profile extruded material : A6063
3) Drawn material: A6063, A5052, A5056, CM10, YM3007, etc.
Surface treatment
Aluminum has some inherent anti-corrosion characteristics due to the oxide film formed on its surface. When wear resistance or an insulating layer is required, alumite is a treatment commonly applied, and Hard anodized aluminum is another choice for much higher strength.
Recently there was extensive news about carbon fiber composite materials used in place of aluminum alloy for the Boeing 787 aircraft body. Due to its high strength and light weight, carbon fiber composite has a bright future with prospects for greater variety of usage in automobile and other industries. However when it comes to availability, processability, and cost, the advantage goes to aluminum. Aluminum will still be the material of choice for many years to come.
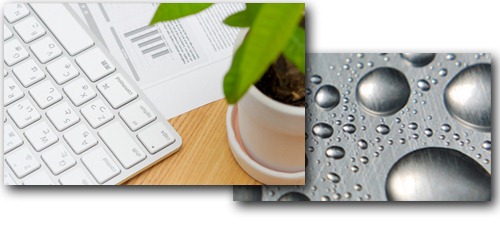